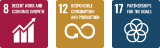
Supplier Sustainable Management
Novatek has formulated a sustainable management strategy for suppliers, incorporated ESG into the risk assessment of supplier management and procurement processes, and conducted supplier evaluations on a regular basis; in response to the United Nations Sustainable Development Goals, Novatek continues to pay attention to issues such as energy conservation, carbon reduction, environmental protection, and pollution prevention, exerting the influence of responsible supply chain.
In order to create a green and sustainable environment, Novatek held its first "Supply Chain Sustainability Forum" in 2022 and plans to hold it again in the third quarter of 2025. Through this event, we work with our supply chain partners to set operational goals, bringing together key suppliers from the wafer, packaging, and testing sectors, both domestically and internationally. The forum focuses on climate change as its main topic, inviting suppliers, experts, and scholars to share insights on international decarbonization trends, waste reduction, and achievements in promoting the circular economy. We hope to strengthen the competitiveness of our supply chain through this forum, as we work together towards the ultimate goals of net-zero carbon emissions and sustainable operations. |
Supplier Sustainable Management Strategy
Mutual Benefits of Partners
Novatek dedicates great efforts into having a positive cycle of IC design and supply chain manufacturing, and apart from establishing cooperative relationships with suppliers to jointly produce highquality and high-value products, we also pay attention to environmental protection and take into account the rights and interests of all workers. With respect to the sustainable management of the supply chain, the Company has adopted the four strategies of ‘Following Procedural Standards’, ‘Risk Assessment’, ‘Monitoring and Auditing’ and ‘Continuous Improvement’. We exhort our suppliers to put their efforts into a business model of social responsibility, to continuously improve and be courageous in commitments, working with dedication towards sustainable development. Novatek plans to formally incorporate a sustainability management clause into supplier procurement contracts in the third quarter of 2025, in order to promote supplier understanding of and alignment with Novatek’s corporate sustainability initiatives. |
|
Novatek Supplier Management Mechanism |
|
Supplier Code of Conduct
Novatek Supplier Code of Conduct
The main suppliers of NovatekNote 1 can be divided into chip manufacturers, IC packaging houses, and IC testing houses. Those wishing to become the suppliers of Novatek must pass the Company’s new supplier assessment procedure, which includes the audit of production capabilities, the audit of operating systems and the audit of quality systems, ensuring that the capabilities, reliability and quality of new suppliers meet the requirements of the Company and customers. Apart from the above considerations, Novatek rigorously evaluates new suppliers based on environmental and social (including human rights) standards. The Company also pays attention to international sustainable development issues and believes that suppliers need to have a certain system to fulfill corporate social responsibility. Since 2022, Novatek used the "Responsible Business Alliance (RBA) Code of Conduct" as its basis for formulating the "Novatek Supplier Code of Conduct" and required suppliers to comply with and sign it. In 2024, Novatek successfully established and implemented a RBA Management System based on version 8.0 of the RBA Code of Conduct. In the RBA VAP audit conducted in November 2024, Novatek achieved a score of 193.8 out of 200, earning Silver Recognition—demonstrating outstanding performance in corporate social responsibility and sustainable development. This achievement included enhancements to the Supplier Code of Conduct and expansion of its scope to include outsourced on-site suppliers stationed within Novatek’s facilities, ensuring full compliance with version 8.0 of the RBA Code. The aforementioned supplier partners, including two newly engaged vendors, completed the signing of the updated Supplier Code of Conduct in 2024, achieving a 100% compliance rateNote 2. Novatek remains committed to working closely with its supplier partners to further strengthen its sustainable development goals.
|
![]() |
Supplier sustainable management performance
To grasp the sustainable development of Novatek’s supply chain, annual surveys and evaluations on major suppliers will be conducted through risk assessments. This will help Novatek identify suppliers with high risks in the economic, social and environmental aspects, and suppliers with potentially high risks will be requested to carry out improvements within a time limit. If the situation is serious, on-site audit and expert consultation will be arranged to provide guidance, ensuring that the risks can be effectively controlled to comply with the management policy of Novatek for sustainable operation. |
Risk assessment 1: ESG management system risk assessment |
Novatek confirms the establishment of supplier management system through the three major dimensions of economy, society (including human rights) and environment, evaluating the risks that the suppliers may face in carrying out sustainable development, so that appropriate countermeasures can be adopted. After the suppliers have obtained ESG system certification, they will be assessed based on the weighting and classified into three risk levels: low, medium and high. Suppliers with low risks (≧60%) will be selected as the candidate for priority procurement. On the contrary, for suppliers with high risks (≧30%), Novatek will provide guidance or assistance through arranging on-site audits or expert consultation. If the target is still not achieved, the procurement will be reduced or terminated. Assessment of supplier ESG management system is divided into three dimensions with a total of 100%. In 2024, the results of the ESG management system assessment for suppliers were in compliance with the low-risk supplier standard (≧60%), and there were no economic, social and environmental risks. In the future, the status of the suppliers in obtaining ESG system certification will be continuously monitored to ensure that the process can meet ESG management standards.
|
Risk assessment 2: Self-assessment questionnaire for sustainability management (RBA risk self-assessment) |
To gain a deeper understanding of the supplier situation, Novatek not only adheres to the “Responsible Business Alliance (RBA) Code of Conduct” but also actively implements RBA-related management systems and training programs within the Company. Additionally, Novatek requires its supply chain partners to conduct the "Self-assessment Questionnaire for Sustainability Management" covering five major areas: labor rights protection, occupational safety, environmental protection, compliance with ethical requirements, and management systems. This process helps Novatek identify supplier adherence to the “Responsible Business Alliance (RBA) Code of Conduct” and assesses sustainability risks. In 2024, a total of 45 suppliers responded to the sustainability management questionnaire, representing a response rate of 100%, and the suppliers’ scores on the “Self-assessment Questionnaire for Sustainability Management” were all above 96 points. In addition to the self-assessment scores, Novatek also reviewed the suppliers’ responses. If the responses to individual items were incomplete or if documents required additional supporting evidence, the suppliers were requested to provide explanations during regular meetings with Novatek so both parties could grasp the risks of suppliers. A total of 9 suppliers have accepted the RBA-verified audit process (VAP) and have corrected the deficiencies during the audit process.
|
![]() |
Supplier Monitoring and Audit |
Novatek, with a sustainable management mindset, has selected 10 companies to serve as its key suppliersNote. The Supply Chain Management Department and ESG Sustainability Committee conduct social responsibility audits of key suppliers through document review and on-site methods, including the auditing items of the Responsible Business Alliance (RBA) Code of Conduct. In 2024, Novatek completed social responsibility audits for all key suppliers, achieving an audit completion rate of 100%, surpassing the set target of 85%. The improvement items for the audits will continue to be communicated to the supply chain and used for guidance. In addition to social responsibility audits, Novatek also communicate sustainable management goals and reviews the sustainability performance of suppliers (including energy-saving and carbon reduction measures and performance in renewable energy) through regular meetings. This strengthens the resilience of the supply chain in terms of sustainable management.
|
![]() |
Sustainable Supply Chain Management Forum
Novatek held its inaugural "Sustainable Supply Chain Forum" in 2022, bringing together key representatives from its supply chain, including wafer, packaging, and testing industries both domestically and internationally, with climate change as the central topic of discussion. The forum invited experts and scholars to share insights on international carbon reduction trends, waste reduction, and achievements in promoting a circular economy. In addition to expressing sincere gratitude to partner suppliers through this forum, Novatek awarded the ESG Excellence Supply Chain Award to recognize suppliers' efforts in sustainable actions. At the same time, Novatek announced the requirements of the "Novatek Supplier Code of Conduct," collaborating with the supply chain to promote greenhouse gas inventory and green operation goals. These goals include increasing the annual power-saving rate by at least 1% compared to the previous year and ensuring zero days of production interruption due to water shortages. A total of 70 participants joined the forum, providing a platform for communication and learning among supplier partners. Looking ahead, Novatek plans to host the Supply Chain Sustainability Forum again in 2025 to further enhance mutual understanding of sustainability issues and risk management capabilities, and to deepen partnerships with suppliers. This initiative will aid Novatek and its supply chain in progressing along the path of sustainable development, creating a more competitive green economy.
Supplier Sustainability Risk Assessment
To gain a deeper understanding of the supplier situation, Novatek not only adheres to the “Responsible Business Alliance (RBA) Code of Conduct” but also actively implements RBA-related management systems and training programs within the Company. Additionally, Novatek requires its supply chain partners to conduct the "Self-assessment Questionnaire for Sustainability Management" covering five major areas: labor rights protection, occupational safety, environmental protection, compliance with ethical requirements, and management systems. This process helps Novatek identify supplier adherence to the “Responsible Business Alliance (RBA) Code of Conduct” and assesses sustainability risks. In 2024, a total of 45 suppliers responded to the sustainability management questionnaire, representing a response rate of 100%, and the suppliers’ scores on the “Self-assessment Questionnaire for Sustainability Management” were all above 96 points. In addition to the self-assessment scores, Novatek also reviewed the suppliers’ responses. If the responses to individual items were incomplete or if documents required additional supporting evidence, the suppliers were requested to provide explanations during regular meetings with Novatek so both parties could grasp the risks of suppliers. A total of 9 suppliers have accepted the RBA-verified audit process (VAP) and have corrected the deficiencies during the audit process.To gain a deeper understanding of the supplier situation, Novatek not only adheres to the “Responsible Business Alliance (RBA) Code of Conduct” but also actively implements RBA-related management systems and training programs within the Company. Additionally, Novatek requires its supply chain partners to conduct the "Self-assessment Questionnaire for Sustainability Management" covering five major areas: labor rights protection, occupational safety, environmental protection, compliance with ethical requirements, and management systems. This process helps Novatek identify supplier adherence to the “Responsible Business Alliance (RBA) Code of Conduct” and assesses sustainability risks. In 2024, a total of 45 suppliers responded to the sustainability management questionnaire, representing a response rate of 100%, and the suppliers’ scores on the “Self-assessment Questionnaire for Sustainability Management” were all above 96 points. In addition to the self-assessment scores, Novatek also reviewed the suppliers’ responses. If the responses to individual items were incomplete or if documents required additional supporting evidence, the suppliers were requested to provide explanations during regular meetings with Novatek so both parties could grasp the risks of suppliers. A total of 9 suppliers have accepted the RBA-verified audit process (VAP) and have corrected the deficiencies during the audit process.
Supplier Code of Conduct
Novatek pays attention to international sustainable development issues and believes that suppliers need to have a certain system to fulfill corporate social responsibility. Since 2022, Novatek used the "Responsible Business Alliance (RBA) Code of Conduct" as its basis for formulating the "Novatek Supplier Code of Conduct" and required suppliers to comply with and sign it. In 2024, Novatek successfully established and implemented a RBA Management System based on version 8.0 of the RBA Code of Conduct. In the RBA VAP audit conducted in November 2024, Novatek achieved a score of 193.8 out of 200, earning Silver Recognition—demonstrating outstanding performance in corporate social responsibility and sustainable development. This achievement included enhancements to the Supplier Code of Conduct and expansion of its scope to include outsourced on-site suppliers stationed within Novatek’s facilities, ensuring full compliance with version 8.0 of the RBA Code. The aforementioned supplier partners, including two newly engaged vendors, completed the signing of the updated Supplier Code of Conduct in 2024, achieving a 100% compliance rate.
Responsible Minerals Management Performance
In 2024, Novatek surveyed a total of 30 suppliers related to manufacturing and packaging services. According to the survey results, 148 smelters have been identified, covering 29 countries. 100% of the suppliers adopted RMI (Responsible Minerals Initiative) approved smelters to provide products that meet the requirements.
Feedback of Customer Satisfaction
Novatek has established the “Customer Application Service Operating Procedure” to ensure that our customers are satisfied with the products and services provided by Novatek, and the internal activation and execution of opinions of customers. The Company reviews and evaluates customer satisfaction periodically in order to propose responsive improvement plans for analysis and improvement based on the management cycle of P-D-C-A. Through participating in regular customer meetings (to receive customer assessment) or customer satisfaction surveys, after comprehensive analysis, review, and feedback, relevant improvement measures are proposed at the management review meeting. Since 2021, the Company has continued to strengthen the front-end management and monitoring of new products, accelerating the resolution of quality issues and implementing corrective actions. In 2024, customer satisfaction reached 97%, surpassing the target of 90%. This shows that the Company has gained recognition from customers in terms of quality management and improvement.